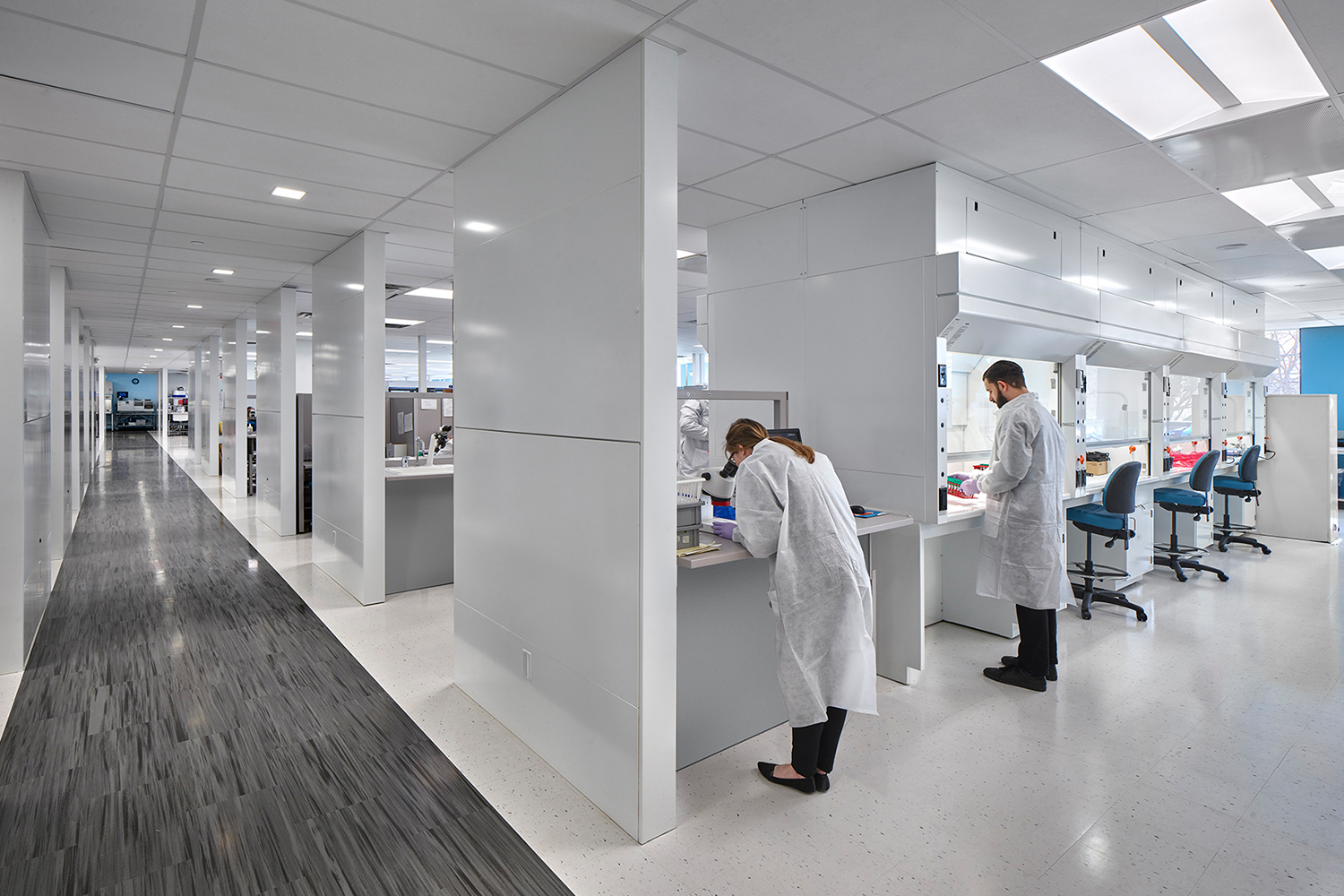
The Lean-Kaizen Method: Creating Continuous Improvement in Lab Spaces
What is it? How does it work? And why is it an absolute necessity in the process of designing labs?
The goal of good design is, at its heart, the presentation of a solution to a persistent problem or set of problems. It is imperative to develop an action plan that methodically engages in discovering the underlying reason of a pain point.
Anyone who has ever had to work in an office, manufacturing facility, or warehouse knows of the obstacles facing teams: interruptions, lack of storage space, crowded conditions, and, poor workflow layouts. When it comes to lab design, though, those issues assume greater importance since missteps can result in serious health impacts. The more time that a tissue sample spends in transit from one area of a lab to another, for example, the greater the risk of contamination. The more often employees’ concentration is disrupted by noise or passersby, the more likely they will make a costly mistake.
As with other types of workspaces, redesigning a lab — even within the same footprint — can reduce many of these situations while streamlining processes and improving safety and quality. But before they attempt to move a station or relocate an employee, designers must take the time to listen.
Effective listening begins by engaging in an honest conversation with the leadership team; everyone must be on board and clear about the organization’s overall vision, mission, and stakeholders. Since the design of the facility should be aligned with these overall values, architects need to fully understand if the organization is in flux or is about to re-direct itself. These preliminary conversations also allow designers to get a sense of some of the specialties of the lab, such as molecular research or transplants, and any design considerations that those specialties demand. At this stage, our team establishes a working familiarity with the physical space and its assets, restrictions, and challenges: including layout, potential for growth, trouble spots, etc.
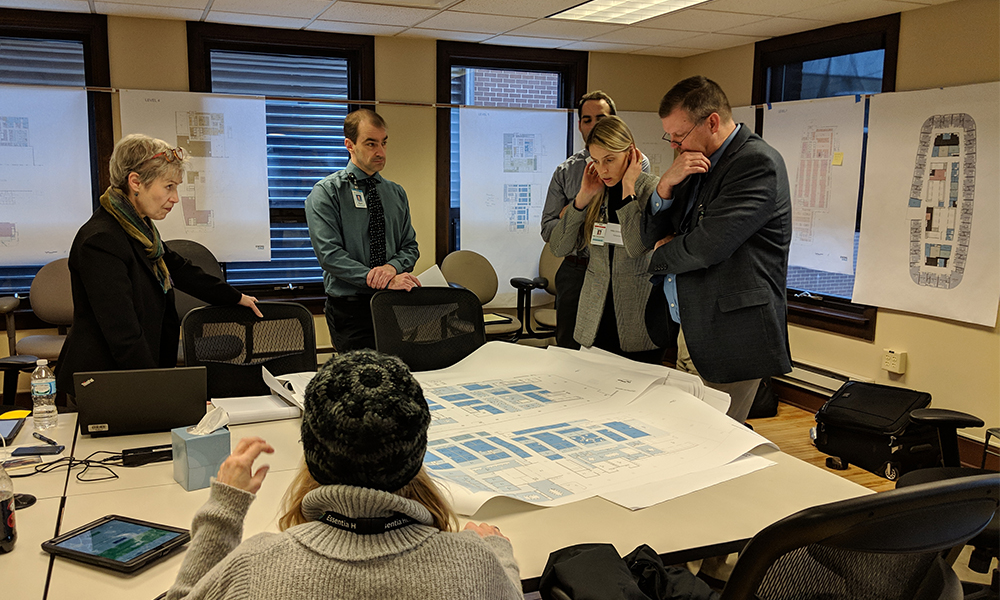
The Most Important Step
Perhaps the most important step is the first one, where our design team spends time talking with and listening to staff members to gain a clear understanding of their individual processes and unique circumstances. In a lab setting, the interviews might cluster employees by their specialties — such as pathologists, blood bank workers, or molecular researchers.
These approximately one-hour interviews aim to get a feel for the obstacles facing each type of client as he or she moves through their physical space. Specific topics include communicating, interruptions, workarounds (such as the need to stack papers on a chair because there’s not enough room on a worker’s desk), and ideas for areas of improvement. Both positive (the ability to easily locate or meet with a team member when desired, good communications with a team member) and negative (frequent interruptions, difficulty in retrieving supplies) feedback is noted.
Armed with this information, it’s time for architects and engineers to visit the lab, to observe, to listen, to build consensus, and to develop simulations — all with the goal of presenting solid, research-driven recommendations.
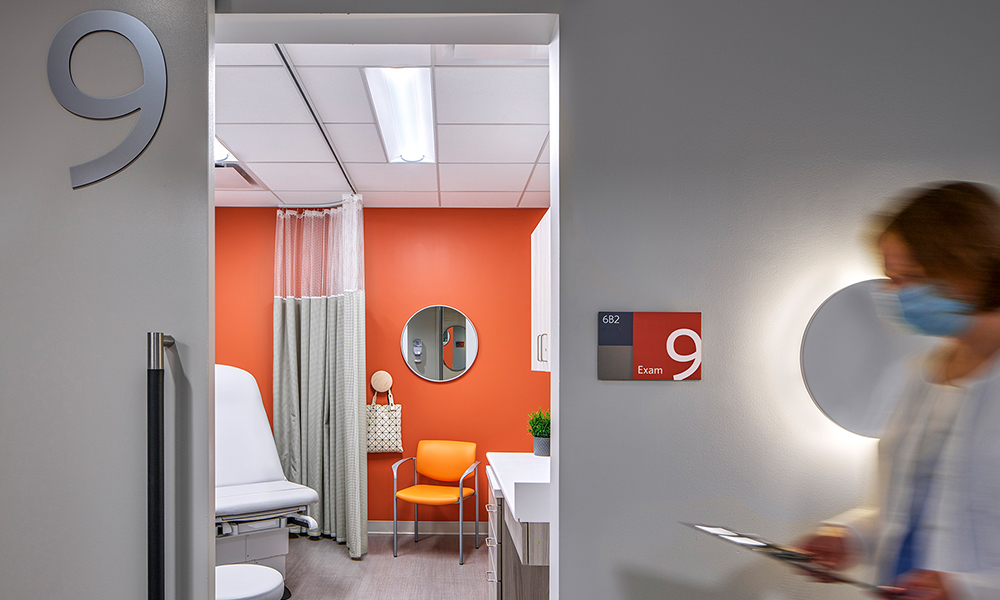
Observe
Using a tablet-based application such as DOTT, EwingCole team members next accompany staff during multiple shifts and on varied days and times to carefully watch how they spend their time at work. The team knows from experience that perception and reality do not always align. One employee might believe he devotes more hours to a specific task than he does, another will forget to account for intermediary steps when clocking her time, and still another will underestimate how often during the day he returns to the same task. During this process EwingCole assesses how people and features of the built environment impact each other. We try to uncover hidden value from space utilization and performance. We will assess frequent interruptions, noise levels, unwanted traffic, storage capabilities, spatial limitations, or any type of hindrance that an employee might experience.
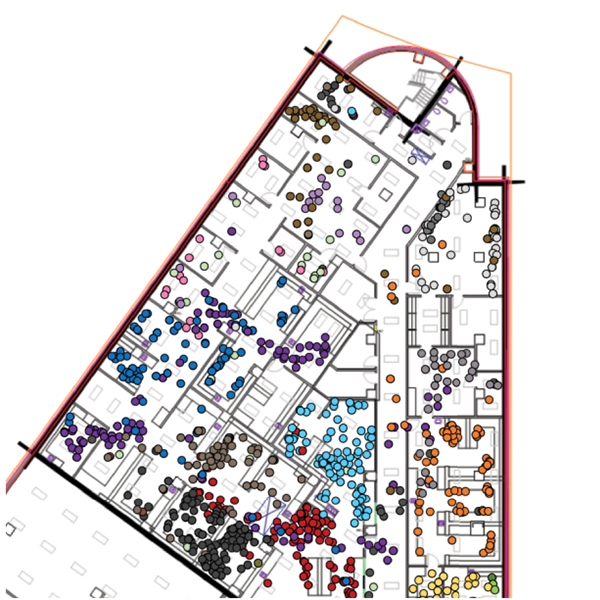
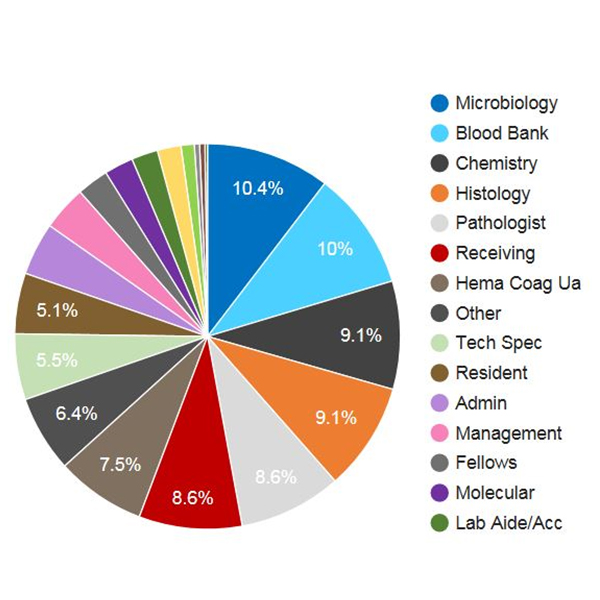
By assigning technicians from each different department a color — blue for blood bank workers, for example, the team will track employees closely as they move about their personal spaces and the rest of the facility. They’ll note how many steps workers take to reach the desired destination, whether anything or anyone gets in their way, what postures they assume, whom they interact with, and which spaces are seldom visited or are underutilized. For one recent project, EwingCole designers recorded 452 such instances (multiple ones for each employee).
Data analysis will reveal specific trouble spots for different groups of workers: one team required more storage, one segment was continually crisscrossing each other, and one set needed to walk in three separate directions to accomplish its varied tasks.
Overall, critical problems like noise, interruptions, unwanted traffic, storage capabilities, workflow, limited workspace, walking distances, and crowded offices were typical. This work represents a discovery process for the client, as well, and can cement a disparity between its goals and the reality of experiences. Before a design team can move forward with redesigning the space, those aspects need to meet and coalesce.
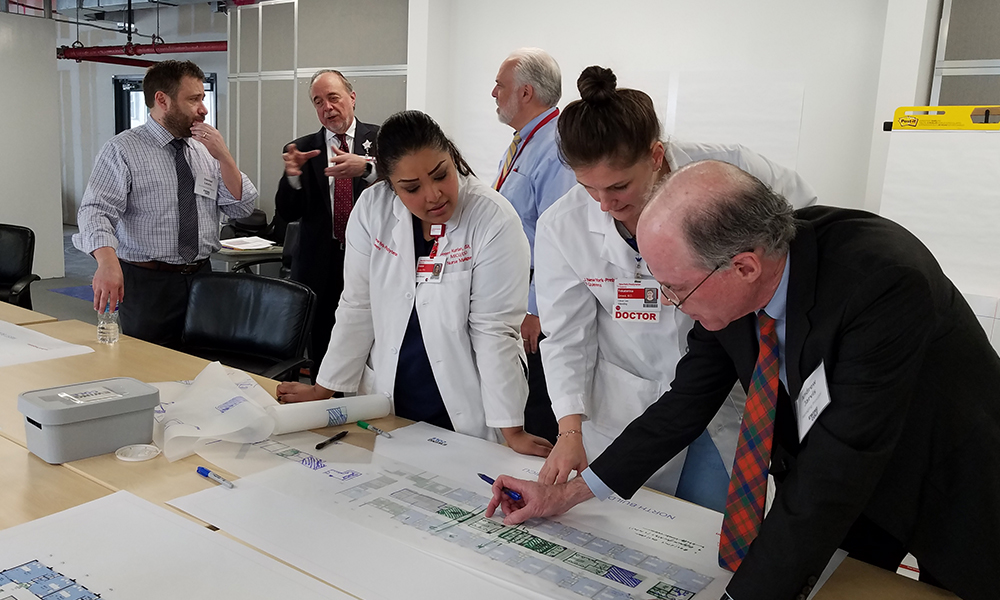
Lean In
To build consensus and arrive at collaborative solutions, EwingCole typically invites representatives from different departments — the lab itself, general administration, and facilities management, for example — to a Kaizen (the Japanese system of continuous improvement) event that relies on lean design principles. The Kaizen event is intended to create consensus among diverse constituencies. The event begins with a presentation to educate the group about Lean principles. Priorities include reviewing specific examples, discussing industry metrics and goals for the project. Stakeholders will be asked to participate in developing operational flow diagrams and similar exercises to better understand the environment as well as implications related to people, equipment, and spatial needs.
For several days, the designers and the staff will work together to develop solutions and design concepts. They will continue to push each other to understand specific issues — what is and what could be. As EwingCole leaders tease out the expectations and requirements of employees and management, they, in turn, illustrate potential space planning options that might help. However, it’s not uncommon for someone to raise concerns that the redesign could cause other problems. Then it’s back to the drawing board. Several design solutions will be developed and discussed.
Eventually, everyone narrows the options to a handful of feasible layouts, which will be objectively evaluated and ranked based upon project-specific goals and priorities. Do some workers get private offices? Should some departments be relocated to a different floor? Is there room to create clear, well-defined paths between workbenches? All these questions and many more will be objectively evaluated and ranked based upon project-specific goals and priorities. All participants will be allowed to vote until one final floorplan is selected.
Model Outcomes
One of the newest parts of this detailed investigation is that we can now simulate the scenarios that come out of the lean design process. Simulation can help us understand the current state and experiment with the future state based on data such as current testing volumes, anticipated future volumes, anticipated turnaround times, demand during peak operating hours, staffing models, and other measurable performance predictors. During this process, we often uncover unexpected operational bottlenecks such as wait times that can be addressed to improve experience and efficiency.
The goal of the simulation is to assess capacity and performance as well as predict the best design solution for the project.
Ultimately, the decision lies with the predictive nature of the modeling tool — it can forecast operational efficiencies in desired outcomes and define how to maximize your existing square footage. It’s the final step in a series of successive steps that act as checks and balances, affirmations, and negations.
Recommendations
The last stage is, of course, for designers to present their recommendations to client leadership. This document re-states any physical limitations (i.e., the space cannot expand, employees must stay together, etc.) and then offers broad suggestions for the reorganization of the area as determined by the lean analysis and the simulation modeling. It also details specific work functions and any solutions, such as improvements to prevent contamination, the introduction of shared space, etc. Finally, designers will suggest priorities, intermediate patches, and outline the development of the project by phases.
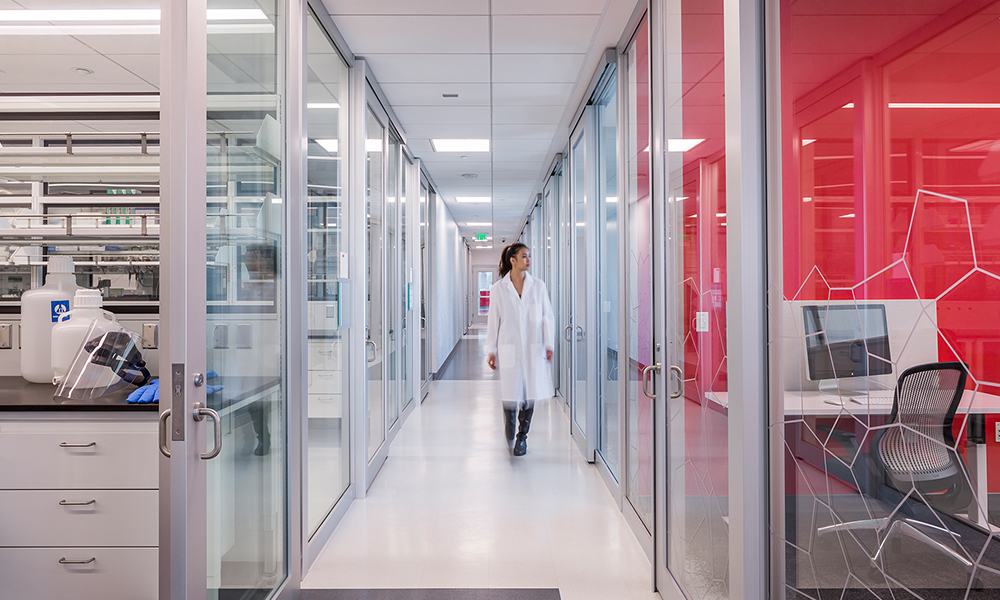
We believe that the more thought put into a design or renovation, the more targeted the outcome is firmly backed up by its considered development of a system that facilitates design thinking. We have used interviewing, on-site observation, lean/kaizen, and simulation modeling on several projects and these methods have proven to reduce travel distances by at least 25 percent as well as increase efficiency while reducing square footage needs by at least 10 percent. The result of this judicious mix delivers better designs and happier clients.