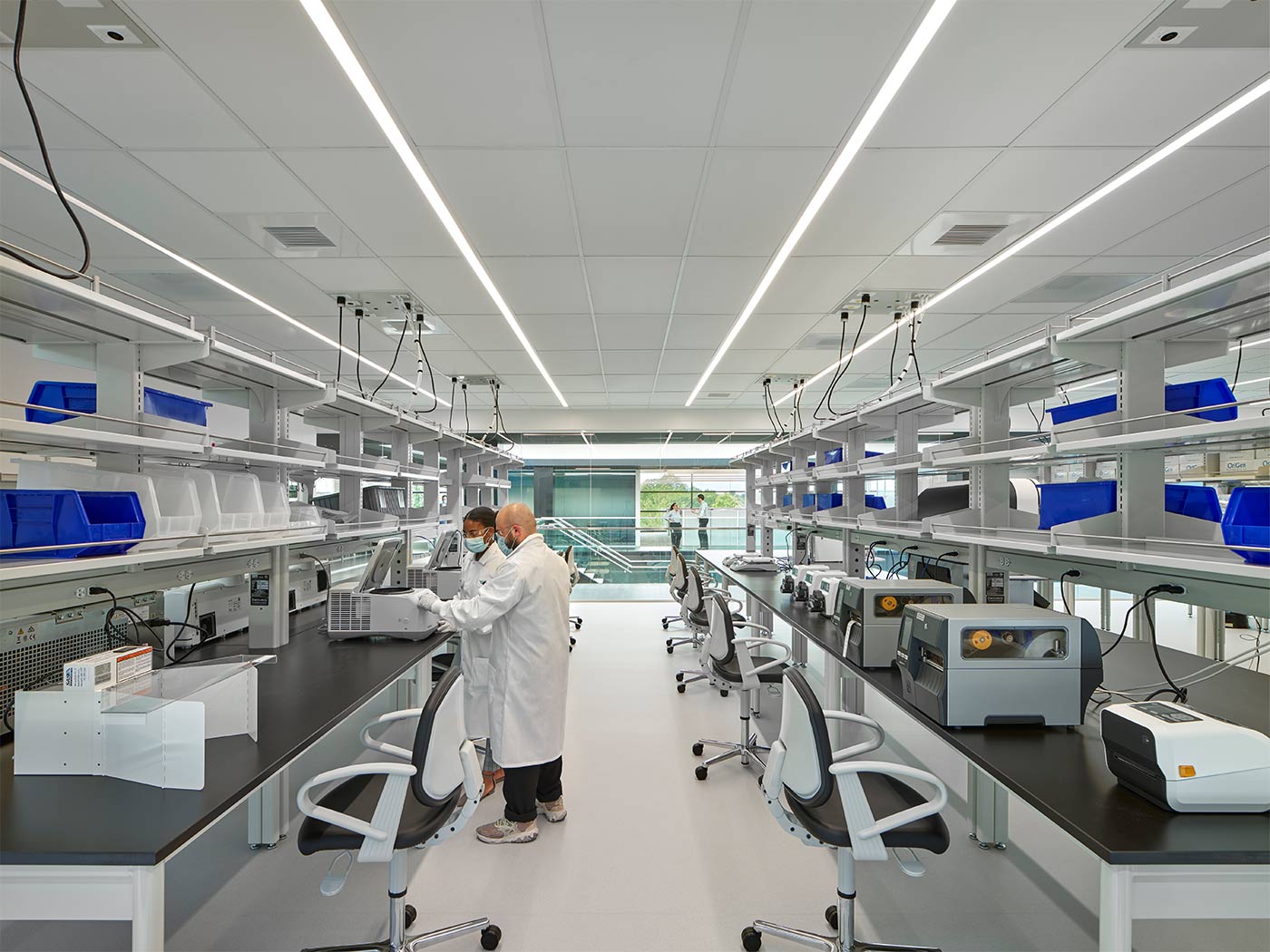
Outfitting America’s Labs to Fight COVID-19
Across the country, public and private sector scientific industries are advancing significant efforts to diagnose, treat, and cure the most contagious viral outbreak the world has witnessed in over 100 years. The COVID-19 pandemic has created immediate market demands for a variety of life science businesses to perform research and diagnostic testing on more hazardous viruses that are unsustainable in traditional wet science or testing laboratories. Many existing labs will require upgrades to meet certain containment levels, such as those set for biosafety level 2 (BSL-2) or level 3 (BSL-3) work, in accordance with the National Institutes of Health (NIH) and the Center for Disease Control (CDC) guidelines. These conversions are, if not already, likely to become routine as both public and private research facilities move to develop, manufacture, and distribute treatment for COVID-19.
Turning Discovery into Health
Government efforts on COVID-19 will continue to be led by the National Institutes of Health, their multiple institutes including the National Institute of Allergy and Infectious Disease (NIAID) division, the CDC, along with many affiliated federal medical and defense research laboratories. The public and private sector mobilization efforts to test and develop a treatment for COVID-19 are robust and swift. Architects and engineers are now being called upon to help shift and outfit clinical testing laboratories and research spaces to accommodate the development of crucial treatments. Our science and technology groups are actively working with the NIH to serve Dr. Anthony S. Fauci’s NIAID and the NCI at several sites, including Fort Detrick, and the Advanced Technology Research Facility (ATRF) in Frederick, one of the nation’s leading centers for biodefense and high containment.
Growing Market Demand for Increased Biocontainment
The design of many of the country’s laboratories is for general life science research with levels of containment consistent with federal guidelines set for biosafety level one (BSL-1) because agents used are not generally associated with human disease. However, laboratories, where the risk posed may foster higher demands for safety and control, must be designed following the NIH and CDC guides for either BSL-2 or BSL-3, where the use of certain microbiological agents poses a health risk, or worse, may cause illness or death through aerosolization or other unknown causes of transmission.
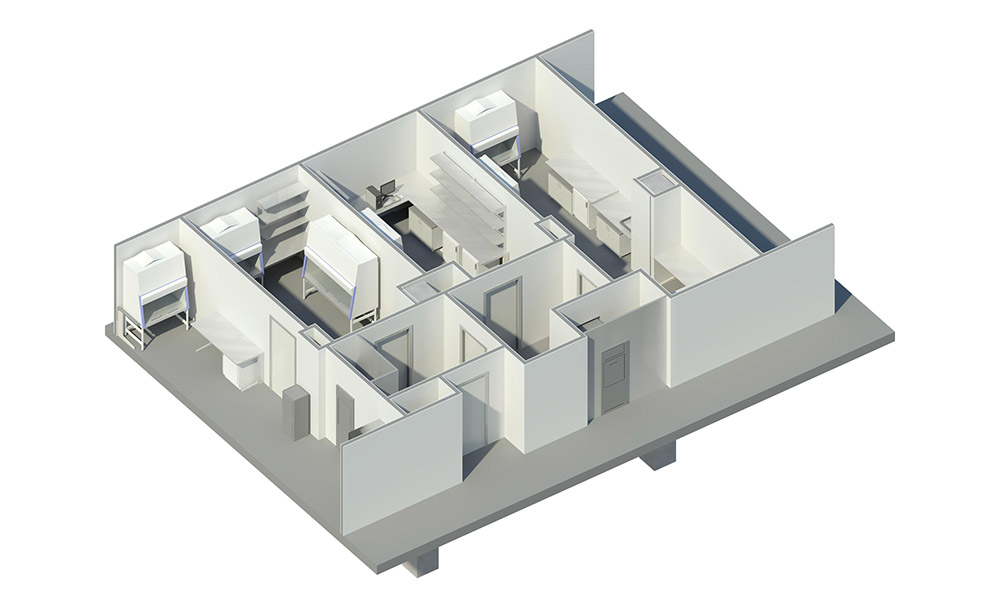
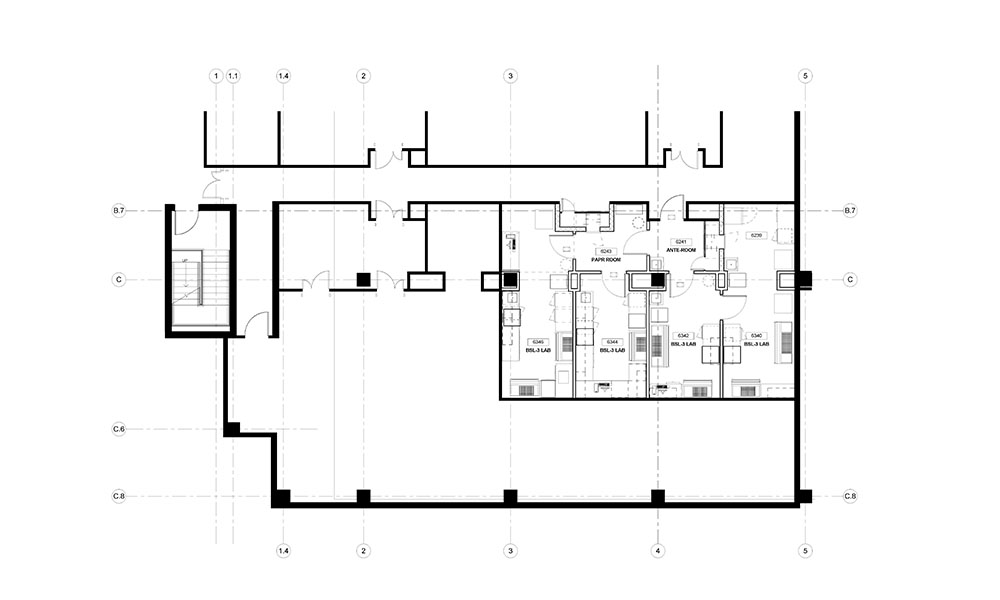
Hundreds of growing life science companies across the country operate in private sector multi-tenant commercial buildings, many of which have been developed within regional science clusters to foster research and development. Others are located in general commercial developments. Significant science clusters have formed in and around major research universities such as in Boston and Cambridge, New York City, the Washington DC metro area, Baltimore, the Research Triangle Park in North Carolina, nearby Wake Forest Innovation Center in Winston-Salem and around Duke in Durham, NC., Atlanta, San Diego, and San Francisco, California. These locations are rich in multi-tenant buildings that can be developed or adapted for use in scientific research, including those used for higher levels of containment and disease research.
Planning for Containment in Testing and Research Labs
Architects have an invaluable role to play in the development, planning, and conversion of viable BSL-2 and BSL-3 testing and research spaces with a speedy and disciplined approach for evaluating facility program parameters and building system strategies.
Understanding the detailed operational requirements of a specific research effort includes a thorough review and understanding of the scientific mission, equipment used inside the active environment, working processes, protocols, etc. Such details build and support the basis for mapping clear facility design programs and translating them into safe, functional, and compliant operations.
Scientific communities engaged in these specialized areas of work will commonly create zones within their laboratories to conduct biological work on cells and/or tissues using biosafety cabinets and other containment or decontamination devices. There are many types and styles of safety cabinets that must be certified by the National Science Foundation and the American National Standards Institute (NSF / ANSI 49). These cabinets, also sometimes known as glove boxes, all serve the same function; they provide maximum protection from hazardous microbiological agents. Class II and III are air-tight, requiring mechanical and engineering systems to provide negative pressure airflow and HEPA filtration systems. These biosafety cabinets are built to restrict airflow from migrating outside of a containment area or setting through a negative pressure air system and HEPA filtration. These are air-tight enclosures constructed with materials that allow easy cleaning and disinfecting in the event of a spill or local accident.
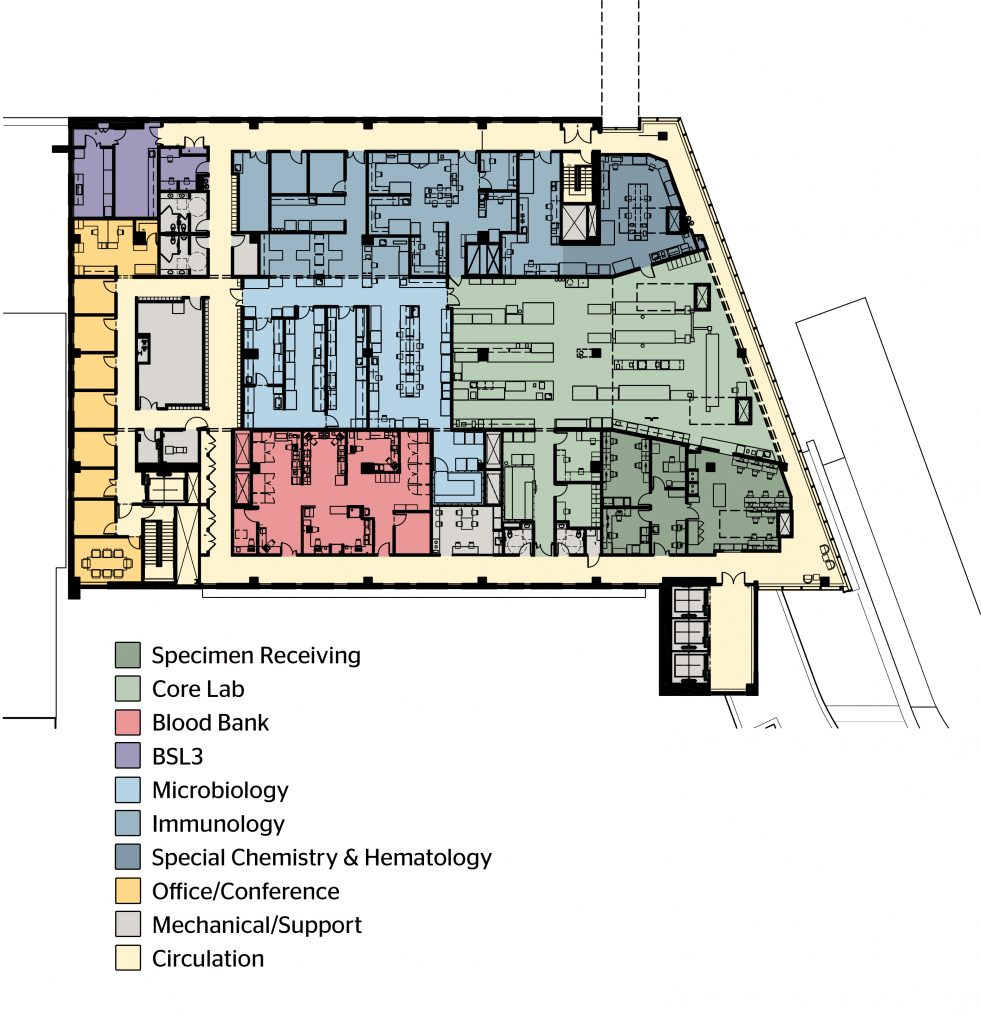
When designing to contain hazardous biological materials, emergency shutdown systems are paramount. Strategies and engineering devices can be set up in design to allow for the emergency shut-down of an operation along with the associated systems, after which the systems are then purged and decontaminated with protocols that can be validated by a third party.
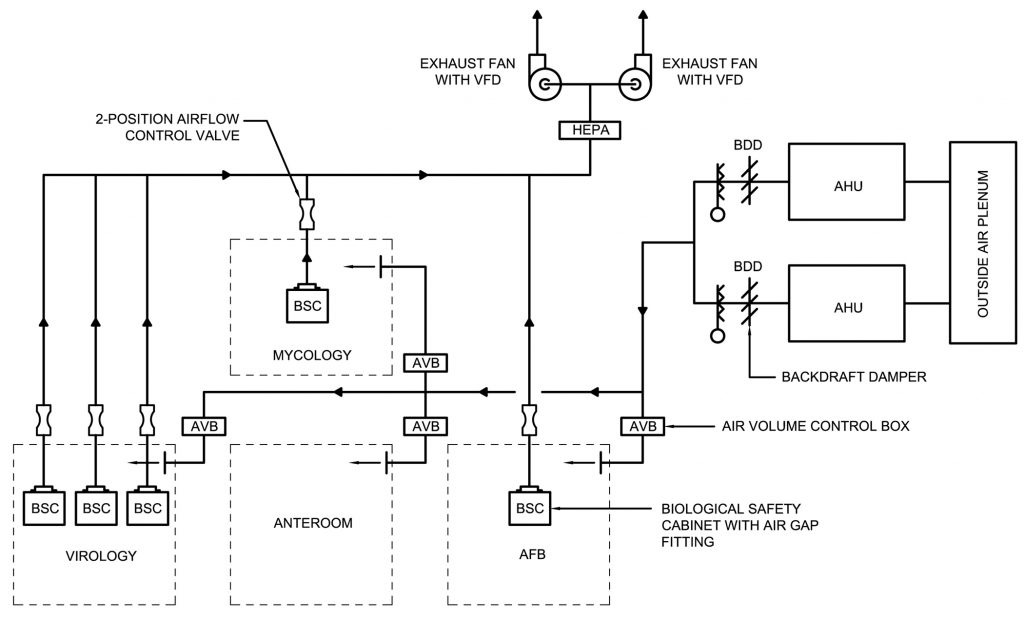
Designing to meet the BSL-2 and BSL-3 requirements for containment include:
- Strategic planning measures which include emergency back-up power for building systems and equipment used in the operational areas
- Provisions for mechanical or electrical system redundancy in the event of mechanical equipment failure for the safe and continuous operations
- Pressurized airlocks to prevent the migration of risk generating activities
- Showering facilities so that personnel can be immediately administered to if contaminated during operation
The design of every facility that requires the incorporation of containment strategies is unique as each varies in mission, risk, and scale of activity. With proper facility planning, design analysis, and engineering controls, following recognized prudent industry practices, these facilities can be successfully integrated into most common commercial building settings.